As 2018 dawned, the excitement in our robotics world skyrocketed – RoboCup 2018 was on the horizon, and the destination was the vibrant city of Montréal, Canada! The road to the tournament was no walk in the park, but fueled by a burning passion for participation, I took a leap of faith.
Having completed five semesters of my bachelor’s, a realization hit me hard – my interests deserved more of my time. So, with determination in my heart, I applied for a semester off. It was a clear choice; to make an impact on my team, I needed to dive headfirst into the world of robotics. And so, my 6th semester became synonymous with Soccer Playing Robotics.
Meet our team, the Immortals – a self-founded group of students from diverse universities. Born in 2008, our team was the brainchild of engineering students who once were our robotics teachers in high school. Our focus? The prestigious RoboCup, specifically the Small Size League (SSL). In this league, teams are tasked with crafting soccer-playing robots capable of engaging with a golf ball. From mechanics to electronics and software, every aspect falls under the team’s purview.
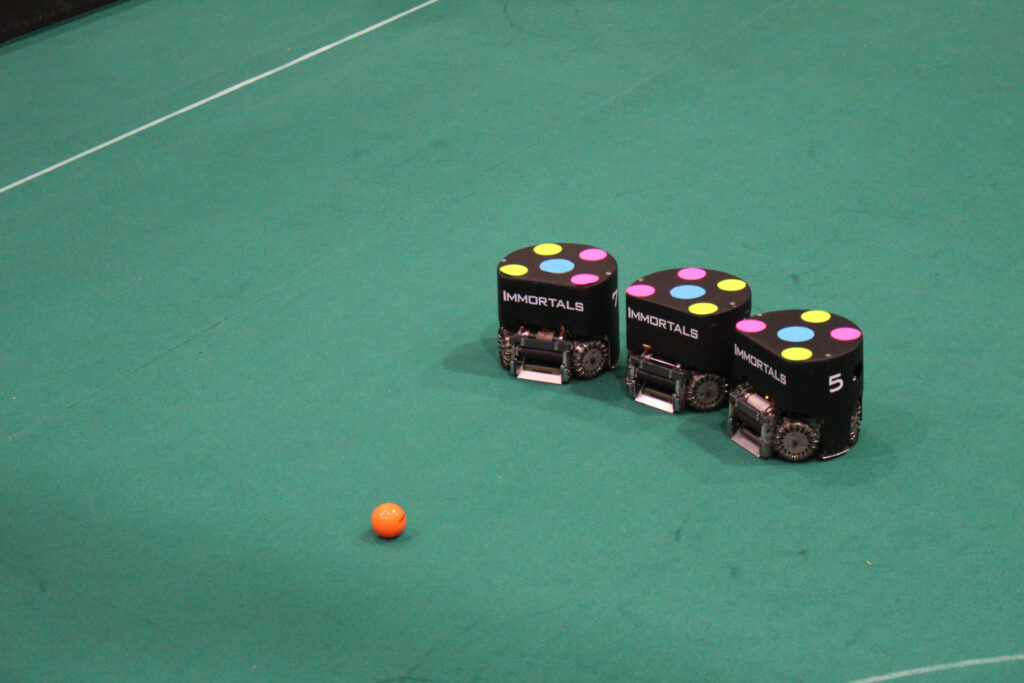
Back in 2016, the reins were passed to us as new team members when we started our bachelor’s studies. The seniors decided to take a step back, transitioning into mentors while we stepped into the frontline. An additional honor bestowed upon us was becoming the next generation of robotics teachers for high school – a tale worth sharing in another post.
Back in 2016, we took our first shot at RoboCup in Leipzig, Germany. It was a big deal for us as we were kind of passing the baton from the older team members to us, the new folks. Everyone was there, the oldies and the newbies, joining forces to guide us through our first-ever tournament.
In those early days, my job was to fix up the circuits of our robots. They took a beating from all the action on the field, and let me tell you, our circuits had some real design boo-boos. They were breaking way too easily. There were also some hiccups in how the robots’ circuits and mechanical stuff were put together. But hey, our robots had this cool design that saved money and made them more reliable, though there was room for improvement.
So, during my break from classes in 2018, I spent about three months refining those circuits. The outcome? A tweaked circuit that now works more smoothly with motors and sensors, includes a handy fault detection feature, and has a slightly stronger processor. Feel free to take a look at the final results below.
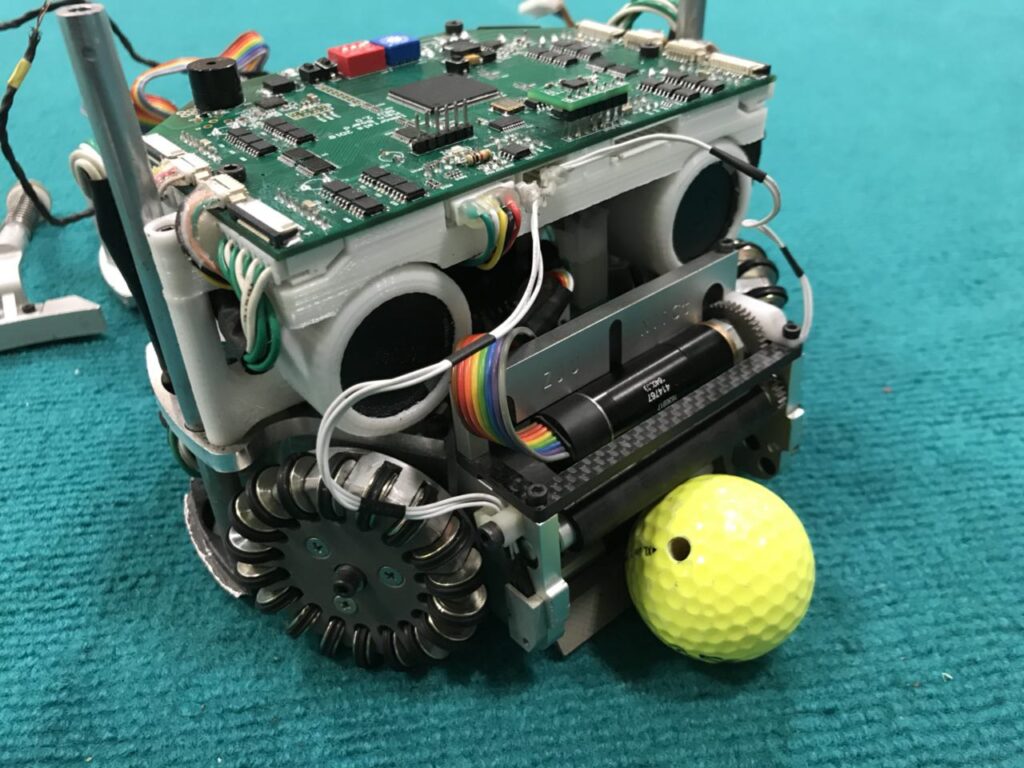
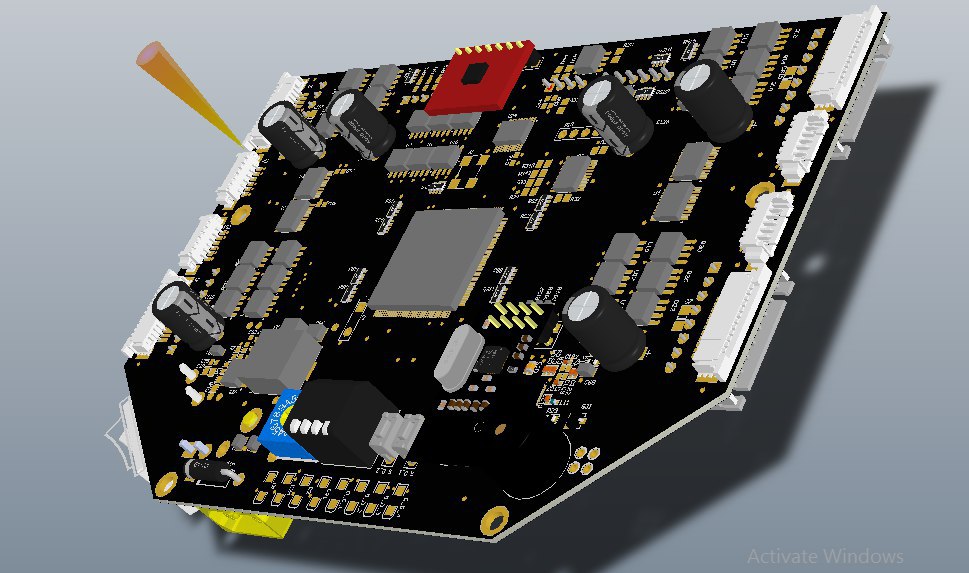
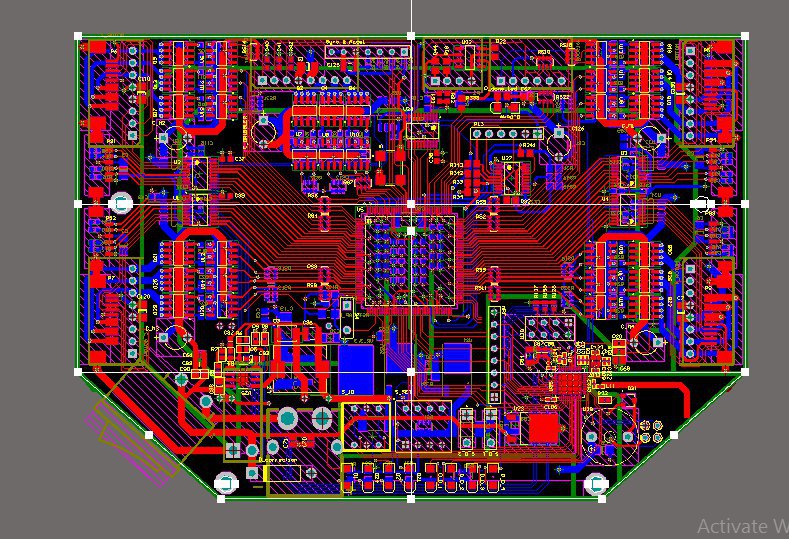

The new circuit comes with an ARM processor and an FPGA, offering several capabilities:
- It can handle up to 5 BLDC motors with a power of up to 50W.
- It supports wireless communication through Bluetooth or Nordic’s Enhanced ShockBurst protocol.
- It can determine its direction using compass capabilities.
- It has the ability to detect faulty motors.
- It controls high-power circuits to enable kicking and chipping capabilities in the robot.
Our robot faced a big problem with its delicate encoder sensors, which are used to measure how fast the motors spin. Each robot had four of these sensors – one for each wheel. These sensors were super important. Without them, the robot would go crazy and move around uncontrollably, like a cowboy trying to ride a wild bull in the middle of a field.
To fix this, I came up with a new kind of sensor – a magnetic-based encoder. It’s a more reliable and precise solution that doesn’t cost much. Instead of the old sensors, which were a bit fragile, we now attach a magnet to each motor. This magnet works with a special circuit that can tell which way the motor’s spinning.
After constructing and implementing the new sensor in our robot, our robots became more reliable and successfully passed rigorous tests under high pressure. This seemingly small change marked a significant achievement for us since repairing a broken encoder sensor used to consume a lot of time and energy. Until now, we haven’t even experienced a broken sensor.
Below, you can see the results of the final work on our new magnetic-based encoder sensor:
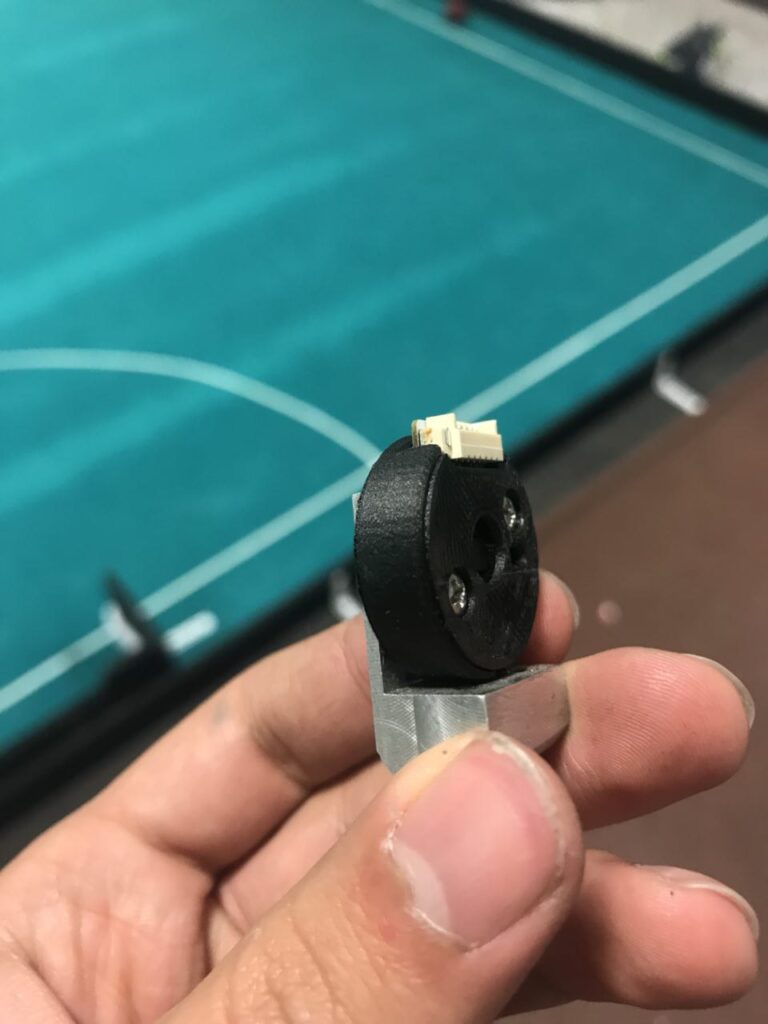
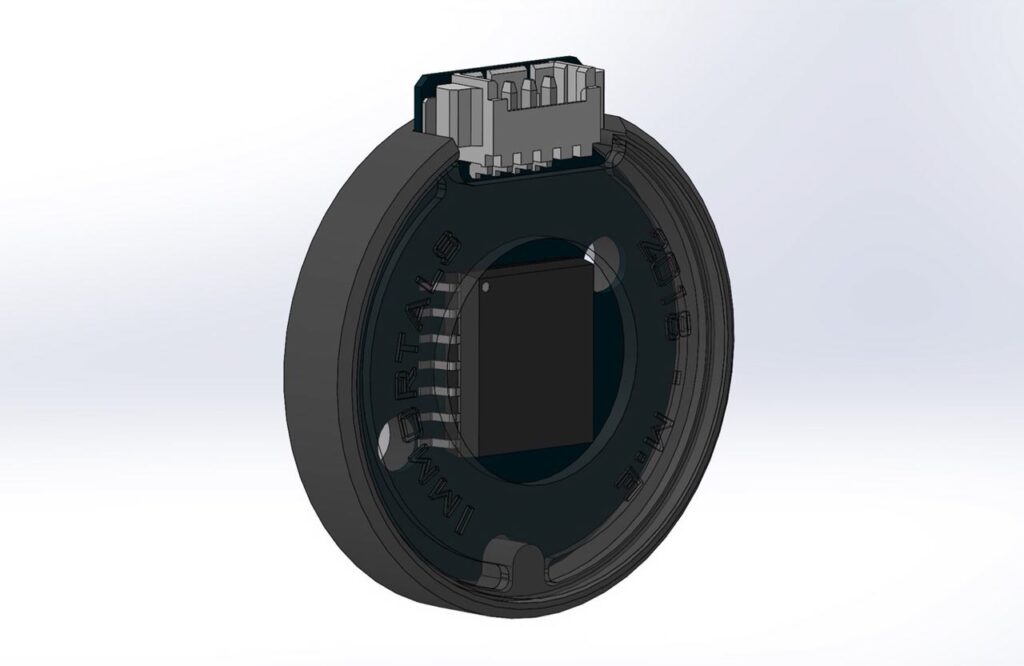
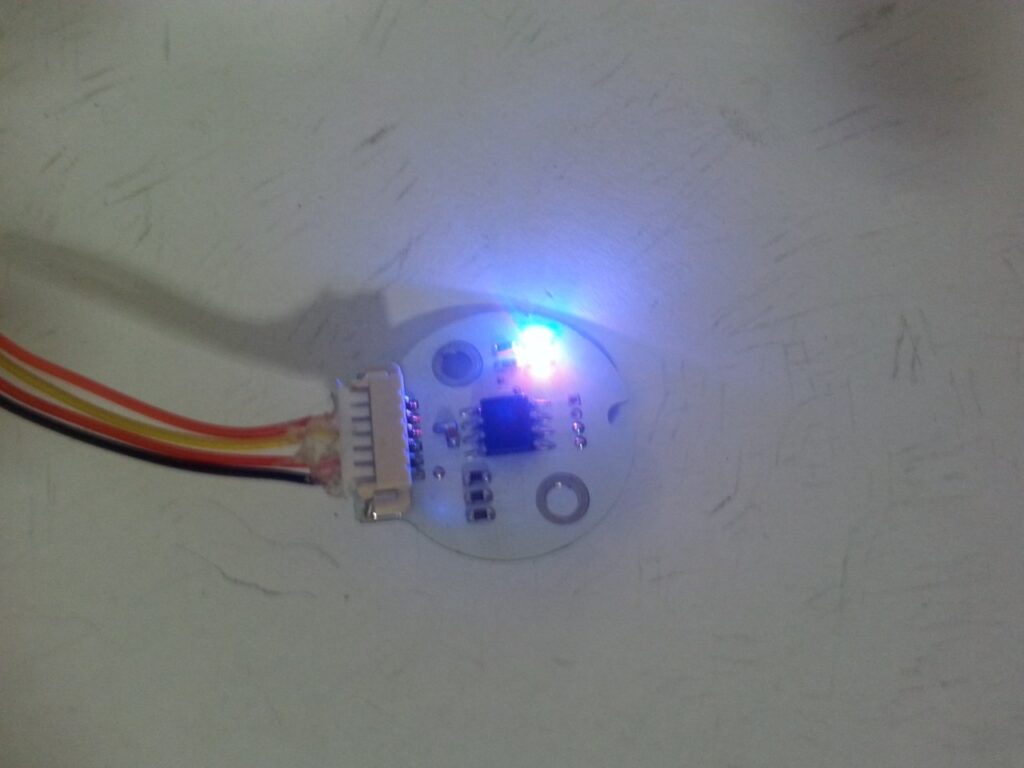
In the end, we made our best effort to upgrade the AI software and compete in the advanced division of the league. Out of 9 teams, we secured the 5th place and also clinched the 2nd place in the open-source tournament. Below, you can watch our robots in action (please excuse the mess in our lab; we were very busy at that time).
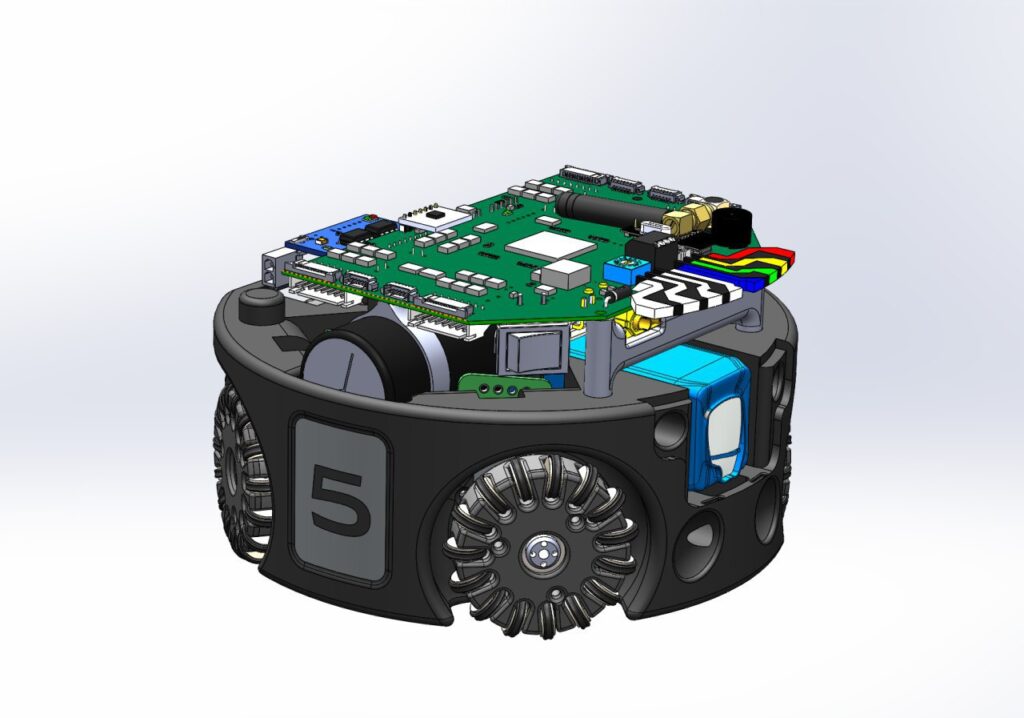
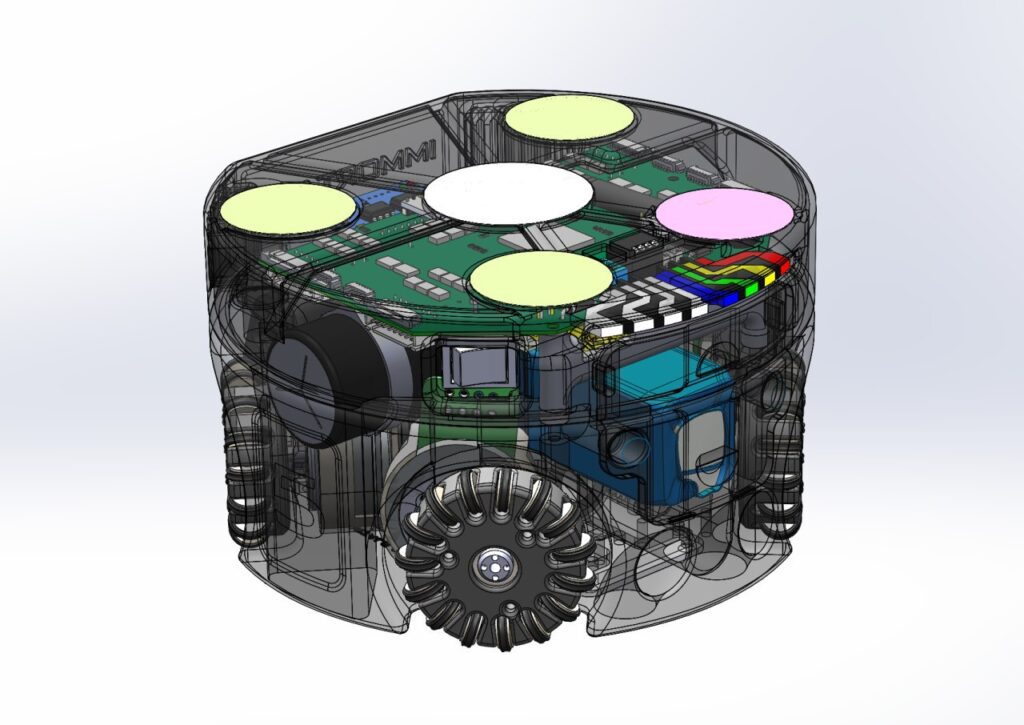
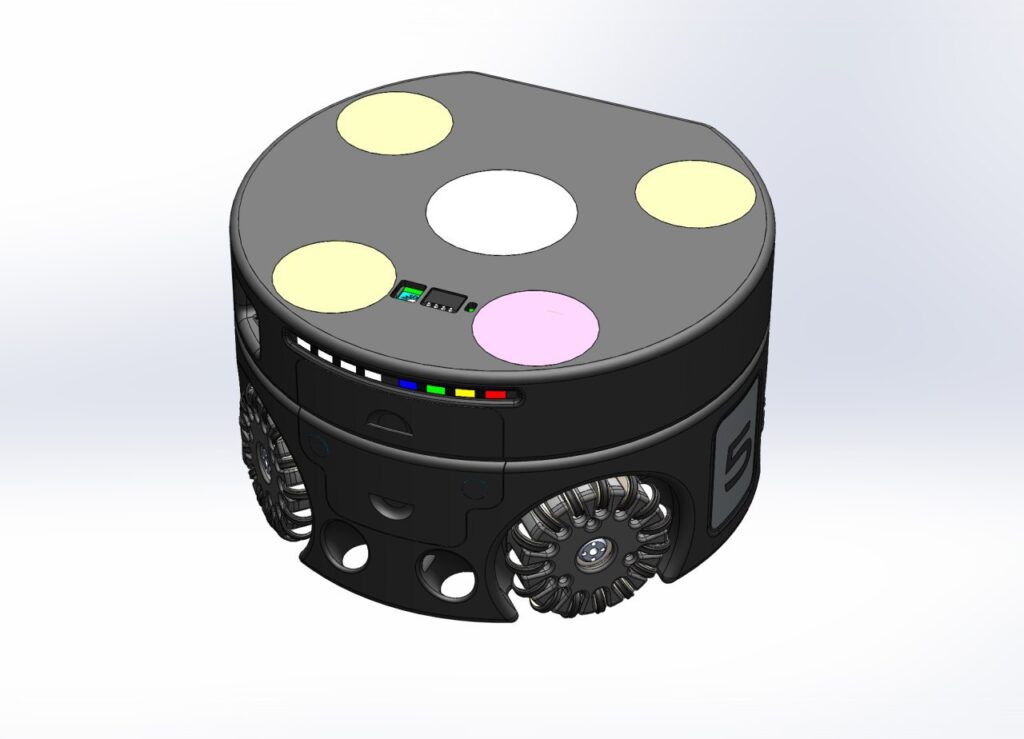
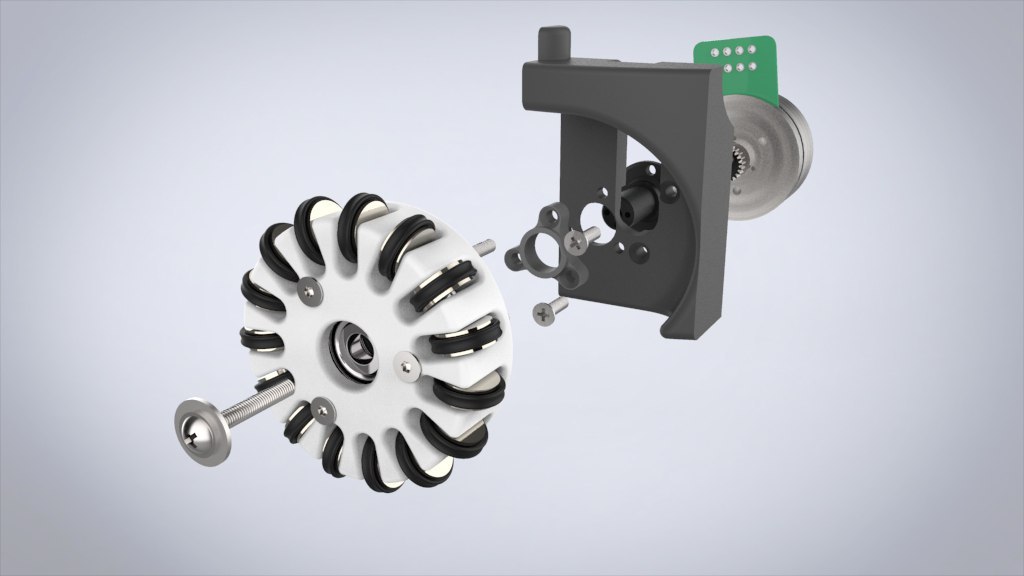
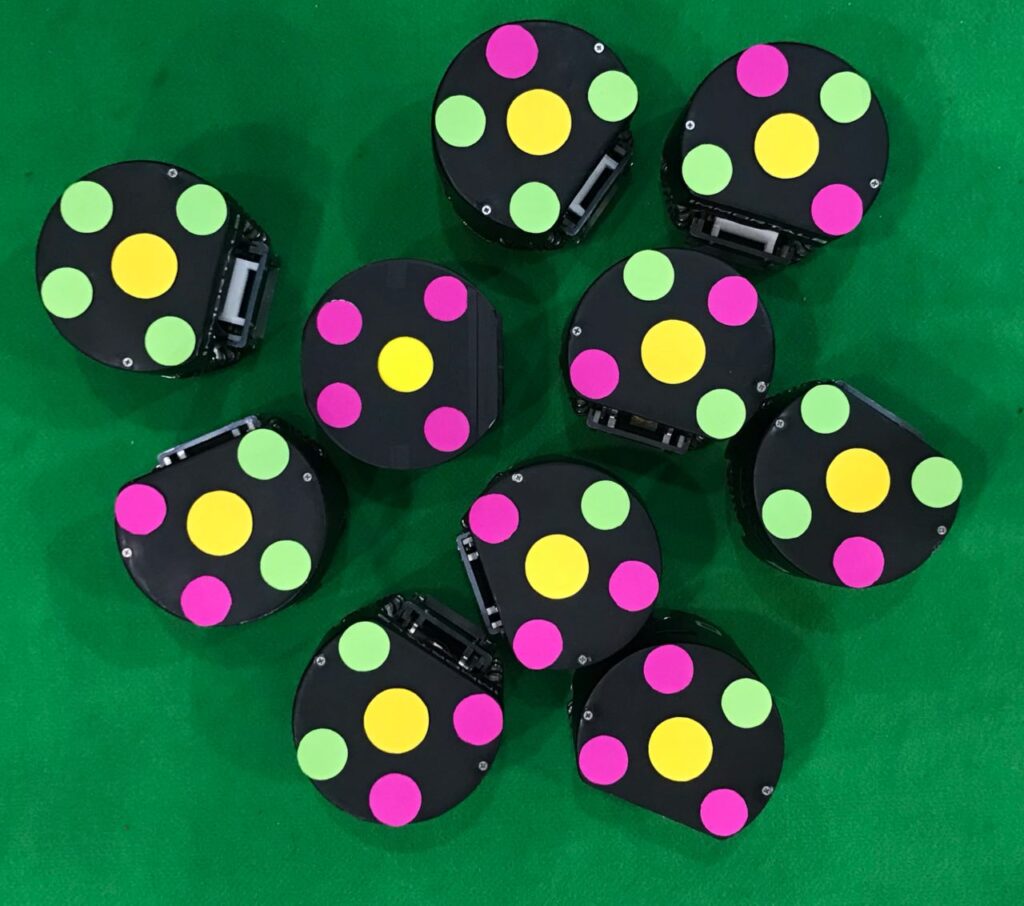
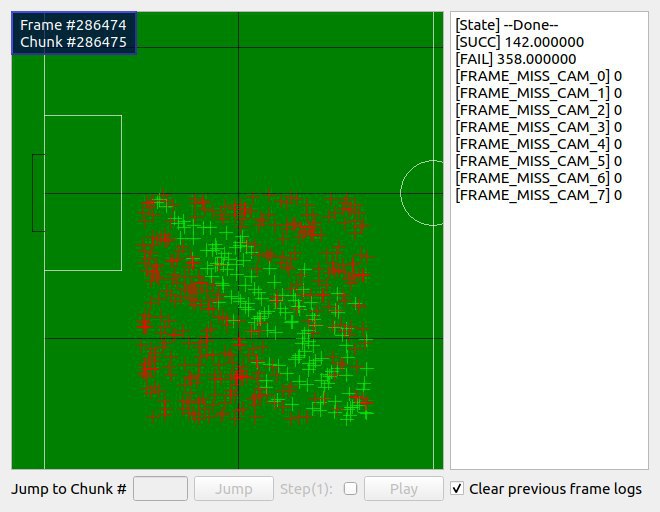
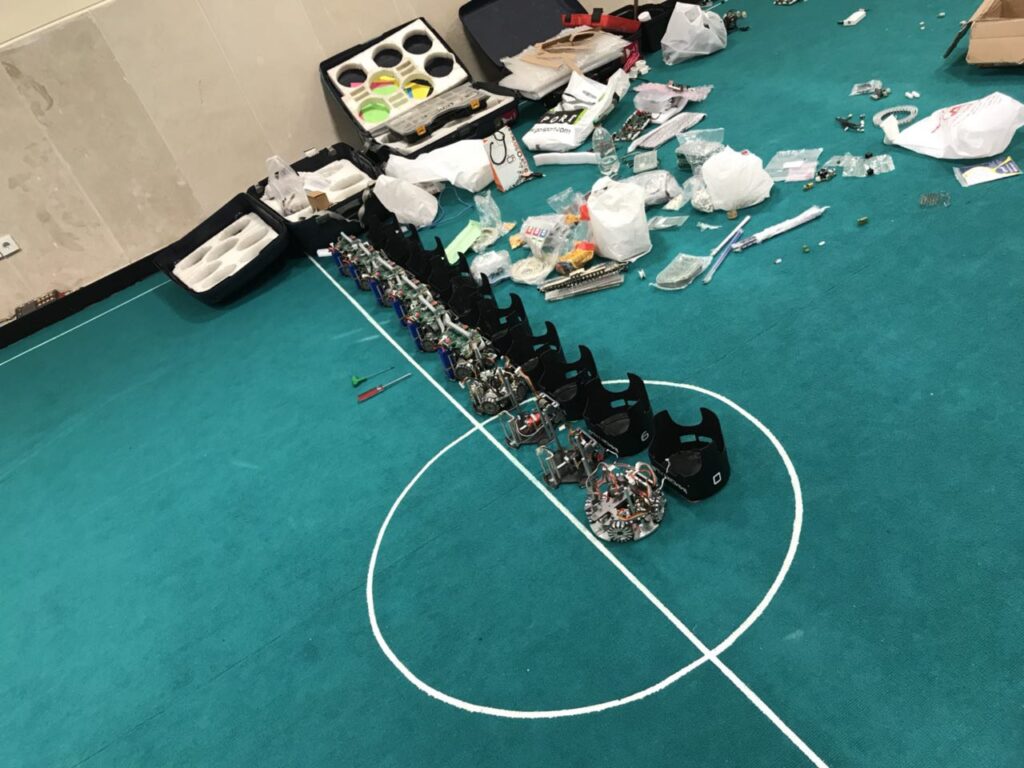
One of our challenges that was live-streamed during that period: https://www.youtube.com/watch?v=Ok2ttRKLdvo?t=6114